Grow Room Design & Construction

Modular cultivation cleanrooms have many advantages over traditional cultivation rooms. Particularly, the enhanced adoption of accessories and components for various stages of processing, packaging and growth cycles. Mother, clone, and flower rooms flourish when room-to-room temperature and humidity are maintained independently.
You bring your lights and plants, we’ll bring the ultimate environment for a pest-free indoor ecosystem with room-to-room control over temperature & humidity.
We simplify grow room construction, installation, and delivery logistics for enterprise organizations. Our ISO 9001 certified controlled environment expertise is endorsed by critical medical-grade and micro-fab facilities throughout the Americas.
Our capabilities also extend to helping commercial growers adapt dirty spaces into medical-grade grows. Our modular grow containments provide tights seals, T-grid lighting mounts, and self-sufficient HEPA air filtration systems.
Send Us Your Drawing!
Your panels arrive prefabricated and ready for installation. The system is affixed to an aluminum anodized frame that supports a full ceiling, lighting grid system, controlled entry, and small team install. We offer installation and project management services for a very reasonable cost. Self-install requires only minimal use of a forklift.
Walls include factory-integrated electrical conduits, air inlets, and exhaust chases, install for HVAC units, fan blowers, and virtually unlimited partitions or bays for the clone, veg, or flower rooms. FRP or vinyl surfaces support vapor pressure control, cleanliness, and will not support microbial growth.
Get a Free Quote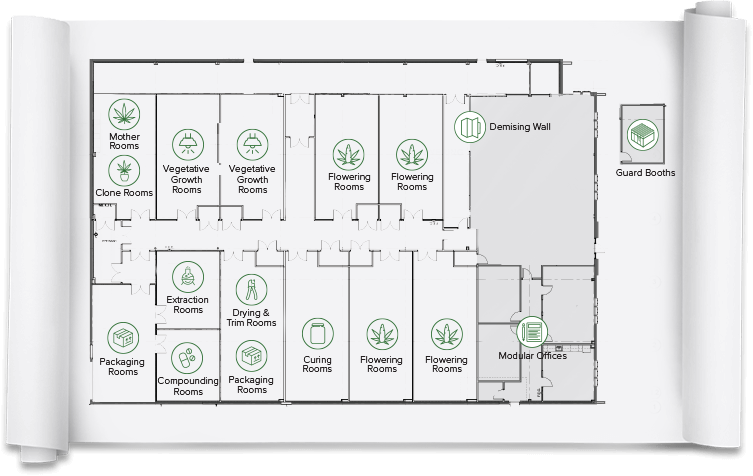
Modular Grow Room Features
Modular grow containment systems shorten construction times while offering more customization and less build complexity. Cannabis grow rooms with modular components ease adaptation of adjacent structures for independent climate controls and parallel production. Environmental control and electrical designs are critical, but so are structural, architectural, and workflow considerations.
Easy Installation
Independent construction of modular cleanroom components allows the removal of grow room walls or individual panels without disturbing adjacent panels, flooring, or ceiling systems. Quick disassembly and the ability to relocate grow rooms reduces labor burdens and favors ever-changing production layouts. Downtime and disruption of adjacent workspaces or grow rooms are minimal. The flexibility of modular designs allows the retrofitting of new structures around previously existing HVAC, electrical, and production systems.
Unique containment rooms for clones, flowers, and seedlings provide environmental controls at each stage of the maturity cycle. Each room is built with prefabricated containment walls self-support the ceilings, electrical, and calibrated for the HVAC system.
Modular Walls & Ceilings
Modular wall panels demonstrate unhindered control over exterior room dimensions and environmental conditioning. Insulation panels with variable R-value help balance cost and prevent over insulation. The ability to integrate electrical conduits, product pass-throughs, windows, ducting, air filters, and storage cabinets closes performance gaps.
A modular installation is faster, requires minimal tools, and requires no sawing or cutting. Scheduled delivery of pre-assembled components allows project management around operation-as-usual. Space and construction staging is minimal.
Air Showers
Air showers prepare cannabis cultivators for grow room entry by pressurizing air to remove any contaminants, mites, or mold spores that cling to garments. They are three primary designs for air showers: a step in step out design, a straight-through design, and air showers for parts and equipment that enters a clean space. The advantage of a straight-through design is that it helps maintain pressure cascades and eliminates flow-through of any invasive particulate. Learn More.
HVAC Systems
Microenvironments within larger structures often lack proper insulation and air conditioning systems. Grow rooms need a lot of air to regulate temperature, air purity, and humidity. In most facilities, air systems consume over 60% of all the site power. As a general rule of thumb, the cleaner the grow room needs to be, the more air it will use.
To reduce the expense of modifying the ambient temperature or humidity, AHU (air handling units) are designed to recirculate about 80% air through the room, removing particulate contamination as is it generated and whilst keeping the temperature and humidity stable. A well-designed air handling system delivers both “fresh” and “recirculated” filtered clean air into the cleanroom so that it flushes the particles more efficiently.Positive Pressure for Medical Grow Rooms
Positive pressure grow rooms elevate room pressure so that outside air is not reintroduced if walls and panels have gaps, seams, and leaks in ceiling fixtures or conduits. Higher air pressure in a centralized room ensures that dirty air from surrounding rooms does not permeate into cleaner spaces, thus helping cannabis growers prevent cross-contamination via air currents or human-borne traffic.
Power Distribution
Power distribution modules provide circuit protection and large-scale device amplification including support for lights and fan filters. Remote air balancing systems route fan filter controls to a central control for macro and micro-adjustments.
Throughout the life of a filter, particulate slowly clogs air passage and air velocity decreases. Small speed adjustments ensure that the growing operation maintains an ideal air exchange and pressure cascade throughout each grow room or processing area. Independent velocity control also extends the life of the filters by eliminating unnecessary airflow loads while also decreasing energy costs.
Frequently Asked Questions
What Components are Included?
- Modular hardwall panels with sealed, integrated windows (as needed)
- Sealed roof-side air plenum for air handling and recirculation
- Vapor and moisture resilient vinyl coated panels, FRP options
- High R-value insulation for retained heat and energy efficiency
- Factory integrated conduits for MEP (Mechanical, Electrical, Plumbing)
- Integrated pre-filter/HEPA/carbon fan filter units and blower motors
- Self supporting T-Grid roof structure for any lighting mount hardware
Advantages over container grows?
- 10' - 20' ceilings provide wider and more natural canopies
- Supports any future CGMP, FDA, medical, and clinical standards
- Positive pressure HEPA system prevents air transported spores
- More efficient per square foot on lighting and HVAC
- Engineered to reduce thermal gradients, eddies, and air turbulence
- Ceiling mounted fan filter units sweep away spores
What information do I need to get a quote?
- A basic drawing or map of the desired facility layout
- Min and maximum ambient temperature/humidity
- Square footage and ceiling height
- Rudimentary values for expected air flow volume
- Power and airflow requirements for per each unique room (veg, flower, seedling)
- Dimensions and requirements for packaging, storage, or office areas
- Dimensions and existing HVAC/electrical output of installation space
What value added services do you provide?
- Includes engineering blueprints after down payment
- Manage all project coordination for CleanPro® Installs
- Install feasible by a small internal team with basic carpentry/forklift
- Controlled entry with fingerprint or card scanners
- Shelving and storage options, lockers & secure storage
What makes these systems world-class?
- Integrated wall channels evacuate the room in a controlled pattern
- Offsets heat loads more efficiently than fan circulated systems
- Constant air velocity sweeps particulates unidirectionally instead of circulating contaminants around the room
- More efficient per square foot on lighting and HVAC
- Engineered to reduce thermal gradients, eddies, and air turbulence
ISO 9001:2015 Certified
ISO 9001:2015 is an internationally recognized standard for Quality Management Systems (QMS). It is designed to provide companies with a set of principles that ensure a systematic approach to achieving customer satisfaction.
Production Automation has implemented procedures to ensure a consistent standard of service for our customers, and customer feedback monitoring to uphold expectations between our vendors, PAC warehouses, and the end-user. We continually conduct internal reviews to ensure that we are always improving.